Blog Archives
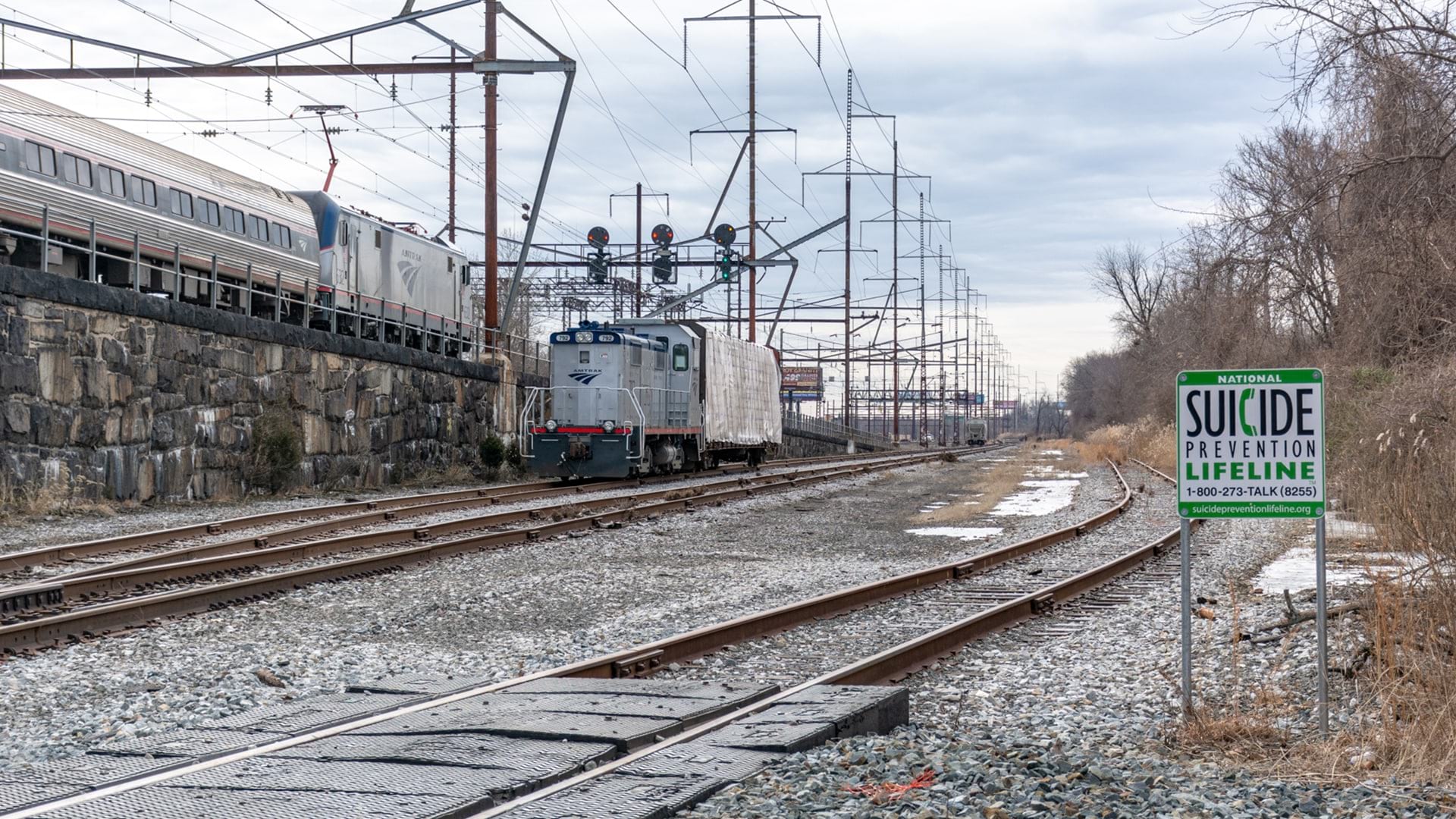
Unseen: How Businesses Protect the Public
With lives at stake, companies are using location analysis to prevent injuries and deaths.
Wherever businesses come in contact with people, they are working hard to minimize hazards and ensure safety.
Spurred on by consumers who demand safe practices from the companies they support—and mindful of the consequences of negligence—pioneering organizations are pushing beyond what is necessary as they find new ways to safeguard the public.
Here we reveal how companies are using technology to see where the public is vulnerable, understand why, and develop strategies to lessen the chance of harm.
Quietly, their work is saving lives.
Article Snapshot: Businesses are increasingly focused on how to ensure public safety. Innovative organizations have found that location intelligence bolsters these efforts by revealing areas where safety measures will have the biggest impact.
Seeing Clear to the Danger
For one electric utility in Australia, 2015 and 2016 were average—and dangerous—years. During that time, residents made 1,400 accidental contacts with the company’s assets: overhead power lines, underground cables, utility poles, and other structures.
Ostensibly, the offenders were civilians and working professionals driving cars, tree-trimmers, grain harvesters, and excavators. But the real culprit was lack of visibility. No one involved in the incidents set out to contact high-voltage equipment. They simply didn’t know where hazards were located before they broke ground on a housing project or maneuvered a tractor around a worksite.
The minor incidents resulted in damage to property. The high-impact events cost lives.
Concerned, managers and executives responded by investing heavily in the utility’s hazard prevention and education efforts.
To help prioritize their outreach to customers and the community, they set out to identify the types of incidents that occurred most often. For that, they needed visibility into the location of all incidents, the contributing circumstances, and the most grievous outcomes. The team enlisted a technology commonly used to map utility networks—a geographic information system (GIS).
GIS created location intelligence by plotting the 1,400 incidents on a map of the company’s service territory—all 300,000-plus square miles of it. For each incident, executives could see the vehicle that made contact with electrical equipment and the type of equipment involved, as well as when it occurred and whether injuries or death resulted. Among other revelations, the analysis showed a high concentration of accidents on farms during months that coincided with harvest seasons.
More Effective Education and Prevention
Knowing that farm vehicles—balers, forklifts, backhoes—frequently hit overhead wires revealed only part of the story. The utility company needed to peer deeper into the problem to see why. Executives turned to artificial intelligence.
On public roads, utility companies can pinpoint where low-hanging wires might cross paths with cars or trucks, and install warning equipment to minimize accidental strikes. But the roads on farms—even large ranches with miles of improvised roads—aren’t mapped in public databases. The utility team couldn’t see the conditions that created the company’s greatest hazard.
They turned to a GIS-based machine learning model to create the visibility they needed. The model paired coordinates of each incident with satellite imagery of the area, and began to spot unpaved farm roads that crossed beneath power lines. With that insight, the team could see what it hadn’t previously seen.
Armed with location intelligence, company representatives fanned out to talk to farmers about safety and install preventive equipment on power lines.
The utility’s GIS also helped staff schedule outreach for maximum effect. The system identified not just the location of farms, but what type of crops they grew. Using that data, the company timed its outreach to precede the various planting and harvesting seasons, when farmers and farm equipment would be most active.
The utility even gave farmers a GIS-based app that revealed electric infrastructure and hazards on their land. Similarly, crop-dusting pilots could access an app to visualize power lines at each farm where they applied treatments.
Through these efforts, the utility helped farmers see—and avoid—dangers that had previously been unseen.
Saving Lives on the Brink
Around the world, suicide attempts are a difficult fact of life on railways.
Germany reports an average of 800 suicides by train every year. In Japan, 6 percent of suicides happen on the rails. In the US, nearly 1,700 people ended their lives on train tracks in the six years leading up to December 2017.
In each instance, one life touches many others. The train conductor becomes an unwitting accessory to death. The victim’s family loses a loved one. Railroad police and first responders encounter a scene that can stay with them for years.
Amid the magnitude of the human tragedy, there are also operational consequences. Hundreds of passengers will be stranded on their journeys to work, weddings, or job interviews. Some may be injured due to the abrupt engagement of the train’s brakes.
Officials at Amtrak, the only high-speed intercity passenger railroad in the US, did not accept train suicides as inevitable. Instead, they have chosen to use data to change the story.
Early signs show it’s working.
Convincing the Skeptics
Barbara Petito didn’t think it would. The Amtrak Police Department’s lead communications specialist thought there wasn’t much that could stop someone bent on ending their life.
“I was not on board in the beginning because I just didn’t know that we could measure any value. And I was not sure that, honestly, this was going to be a method to eliminate the incidents of suicide on the railroad,” Petito told WhereNext.
But Amtrak chief of police Neil Trugman was convinced the company needed to take action, and a colleague named Michelle Jennings had already begun using data and location intelligence to assess the situation.
When Petito got involved, she found Jennings hard at work, using GIS technology to spot unseen patterns in the data.
Grim Trends Emerge
With approximately 87,000 daily riders, Amtrak runs the equivalent of a midsize city—if that city were spread across 46 states, hundreds of stations, and 22,000 miles of track. The same crimes that happen in a city happen throughout a rail network: vandalism, disorderly conduct, theft.
Amtrak’s police department had been using GIS for years to understand and mitigate those incidents. Jennings and the team routinely created hot-spot maps of crime and steered Amtrak officers toward places where preventive policing might yield the biggest impact.
Now she was using the same technology to understand where suicides occurred. Through GIS, Jennings identified the exact location of every pedestrian incident and—by collating additional information such as coroners’ reports and video feeds—determined whether the event constituted a suicide.
She plotted all the events on a nationwide map, and patterns emerged. Clearly there were clusters—places where two or more people had committed suicide. The highest concentrations were in Florida, Illinois, and parts of California—the Bay Area and southern portions of the state.
Officials wondered why.
As Jennings deepened the GIS analysis, she saw clues: Some areas lacked fencing to keep pedestrians out. Other locations were close to homeless encampments near the tracks. In Carlsbad, California, a mental health facility sat near the site of several recent deaths.
By 2017, the investigation had revealed 150 sites—100 along tracks, another 50 at stations—where multiple suicides had taken place.
Using Data to Change the Course of a Life
Petito, her skepticism dimmed slightly by the insight she saw on the map, set to work. Her opportunities for action were complicated by the fact that Amtrak owns fewer than 1,000 miles of the 22,000 miles of track it travels; the rest it accesses through agreements with host railways. But through its own actions and the help of its rail partners, Amtrak worked to install access barriers where it could, and directed its officers to patrol other high-risk areas in hopes of deterring suicide attempts.
Still, many rail lines run on street level and cross pedestrian areas where physical barriers aren’t possible. So Petito and team also invoked a more direct tool. With guidance from Jennings, they installed suicide prevention messages in problem areas. About the size of a stop sign and visible even at night, the signs include the phone number of the National Suicide Prevention Lifeline (800-273-8255).
Petito knew just where to place them, thanks to Jennings’ analysis.
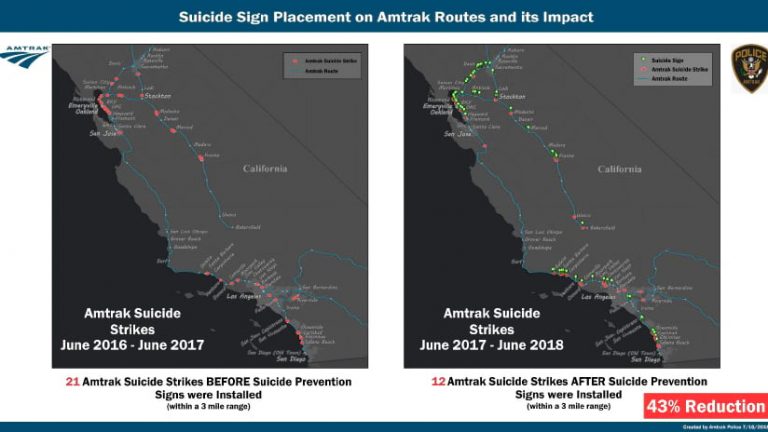
“If you have 22,000 miles of railroad and you’re just putting these out there willy-nilly, I’m not so sure you would have any kind of success,” Petito explains. “We’ve been able to place signs in the exact areas where these strikes have occurred.”
To the relief of Petito, Jennings, and all Amtrak professionals, the increase in the number of signs (222 at last count) coincided with a decrease in the number of suicides on the company’s tracks. From a total of 84 in 2017, the number dropped to 56 in 2018. In specific regions like California, the total went from 21 suicides in the year before the signs were installed to 12 the year after, a 43 percent drop (see image above).
Petito says she’s been heartened by the results, although she and Jennings caution that there’s no definitive proof the program alone is responsible. Still, “there’s a certain percentage of people who are attempting to commit suicide, that see a sign like this, offering help, offering an alternative, [and] they will respond to it,” Petito says. “So that’s what I can say may be happening here.”
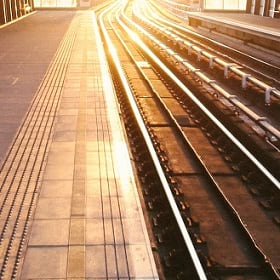
In my mind, this is a success. I don't know if scientifically it could be documented as such. But if someone's responding to this, thank God we've done it, and I applaud the host railroads that have agreed to work with us on this program.
Barbara Petito, Amtrak
Seeing as a Company Grows
Creating visibility across 22,000 miles of track, 300,000 square miles of utility infrastructure, or a sprawling network of stores and offices can be a daunting challenge.
For Amtrak, the utility company, and many other organizations, GIS technology is producing location intelligence that helps decision-makers see problems clearly and understand how to react.
At Amtrak, it turned Petito into a believer.
“There is no question that without that technology, I wouldn’t even begin to try to claim any kind of success for this program.”
This article was originally published in the global edition of WhereNext.
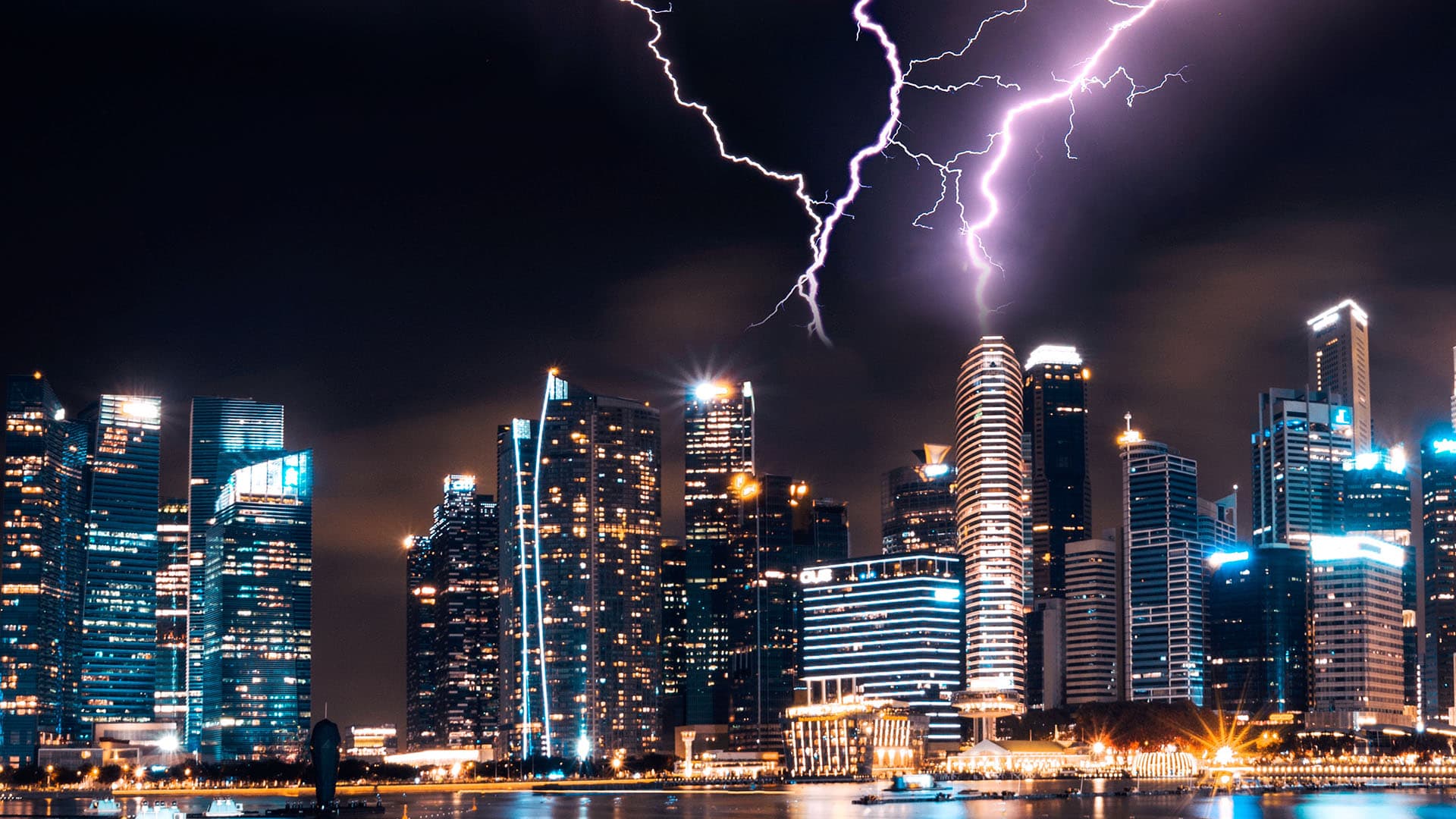
Changing Hazards Prompt Insurers to Rethink the Location of Risk
To ensure their risk assessment reflects risks on the ground, insurers and reinsurers are increasingly relying on location-based risk analysis.
Recent headlines about climate change make it difficult to bury one’s head in the (rapidly receding) sand.
In 2018, a total of nearly 400 natural disasters caused US$225 billion in damage worldwide. The insurance industry covered $90 billion of those losses, according to reinsurer Aon. For historical context, consider data from the Brussels-based Centre for Research on the Epidemiology of Disasters: In the last half century, the number of natural disasters worldwide has risen more than 450 percent.
Concern over the financial effects of weather events has rippled through other industries, including financial services. In a post titled “Hedging Climate News” on the Harvard Law School website, several finance professors outline a strategy for hedging against climate-based risk.
Viewed over a longer horizon, the numbers are staggering. Total global economic losses from natural disasters between 2005 and 2015 were more than $1.3 trillion, with direct losses in the range of $2.5 trillion since 2000.
The insurance industry is evolving from generalizations about location-based risk to sophisticated risk scoring based on GIS-powered location intelligence.
While scientists work to assess the fate of the planet, insurance companies are dealing with the immediate and long-term consequences and costs of climate change. Increasingly, insurers of all types are using location intelligence to get a more complete picture of risk at each property, across supply chains, and across portfolios.
The reality for insurers is that understanding risks specific to location matters greatly, and is key to reliable risk assessment and pricing models. Without accounting for the context of location, insurance companies put themselves at risk. And as the insurers of last resort, reinsurers face even greater exposure. They are the final entity in the chain of climate-change-related liability; the buck stops with them.
More Transparent Risk Analysis
Andreas Siebert, head of geospatial solutions at global reinsurer Munich Re, says the realities of climate change are making Munich Re’s underwriters hungrier for data that can provide both a holistic and fine-grained picture of climate-related property risks.
“We try to keep our clients insurable in the future by supporting them with not only the financial strength of Munich Re but also our knowledge and experience,” Siebert says.
Like other insurers, Munich Re needs highly granular data upon which to base its risk pricing, as well as greater transparency into how risk-related decisions are made throughout client supply chains. Increasingly, that means relying on location intelligence powered by a geographic information system (GIS), which maps, analyses, and models risk for a property and its surrounding area.
“More transparency means a better understanding of what the industry is insuring these days,” Siebert explains. “We have to learn more [about building] construction types, occupancies, the age of buildings—a lot of additional data. We have to bring it together to have the full transparency when we are doing risk assessment.”
For Munich Re, there is a tight linkage between business intelligence and location intelligence. “We are on our way to fully integrating both worlds,” Siebert says. “For us, it means we have direct access to the operational data, which we enrich and analyse with the capabilities of geo-analytics and other dashboard methodologies.”
Munich Re is bringing easy-to-use tools with geospatial capabilities to its underwriting practices. Since the underwriters are not geospatial experts, the tool has to be especially user-friendly and accessible.
Seeing Risk with More Precision
Until roughly the 1980s, the insurance industry did not think at a detailed level about the link between risk and location. That has changed dramatically. NatCat models, for instance, now compensate for the fact that areas that weren’t prone to wildfires are now hot zones.
With GIS-driven location intelligence, the risk profile is much more granular, examining questions such as, “How has this home in this neighbourhood been affected by wildfires and other risks?” Smart maps provide an immediate and compelling illustration of that risk.
Such location intelligence helps drive “point-based risk scoring,” which gives underwriters a more complete view of a property than they have traditionally had. Insurers might take into account everything from local soil composition to the types of trees in a nearby forest (since some are more fire-resistant than others), as well as age and type of property (and a long list of other factors) to arrive at a point-based risk score.
Location intelligence helps unify disparate data relating to a property and its type of risk, whether that is flood, hurricane, wildfire, hail, tornado, earthquake or other calamities. A holistic risk profile also includes threats such as terrorism and civil unrest. In fact, a small cohort of specialists—companies such as CONIAS Risk Intelligence—supplies multinational corporations with GIS-driven insight on where those risks exist, and to what degree.
The location intelligence these analysts deliver can affect multimillion-dollar decisions on how a supply chain is organised and which markets a company serves.
AI-Based Risk Scoring
Using GIS-based location intelligence, insurers have identified risks that appear counterintuitive, but actually reveal new realities. Case in point: Many Californians are not required to have flood insurance because most homes there are not in 100-year floodplains. However, one of the greatest risks in the last five years in California is flooding.
This seems strange for a state that has been in a drought for eight years. Yet, an analysis of location-specific factors reveals the culprits: soil composition, the amount of concrete, the lack of drainage, aging infrastructure, and the type of rainfall events increasingly common to California. In short, there’s more pooling of water and more flooding because the water has nowhere to go.
Location intelligence provides insurers a more nuanced and fully faceted picture of risk, rather than a simple “yes” or “no” answer to the question, “Is this property in a floodplain?”
GIS can quickly analyse those events and produce a risk score for a specific property or a dashboard reading of green, yellow, or red. According to Siebert and others in the industry, the process of data correlation and scoring is becoming automated through artificial intelligence (AI)—specifically machine learning (ML), which is trained to see patterns in large volumes of data. Going forward, all an underwriter will need to do is input an address, look at the score, and then only review a policy if it is automatically denied or flagged for more review.
Munich Re is doing location-based risk analysis, both internally and as a service for clients. For example, its NATHAN service—the Natural Hazard Assessment Network—helps companies assess the risks of natural hazards around the world, from location-based individual risk through to entire portfolios of assets.
“We combine data on global natural catastrophes and enable the user to upload their [property] portfolio to have a very complex and flexible location-based analysis,” Siebert says. Even professionals who don’t work with GIS—including claims managers and underwriters—can input an address and understand its risks, Siebert explains.
A Wealth of Imagery
In the insurance industries and across the business landscape, torrents of location-specific data are pouring in from new sources, including satellite images and aerial photography. Munich Re uses some of this imagery to better monitor storms and evaluate other extreme-weather events. The high-resolution images now assist claims adjusters and engineers in calculating losses on a per-building level.
This is another instance where location intelligence and business intelligence merge.
“We are working in a very tight collaboration with our data analytics teams,” Siebert says. “We want to integrate geospatial tools and functions in our data lake to enrich more of our common data sets with geo-referencing and analytical capabilities. So often, geospatial data is the glue between the different entities.”
As a reinsurer, as well as a primary insurer, Munich Re is keeping a keen eye on what Siebert calls “accumulation control”—using location intelligence to identify where it has the highest potential for losses. “This is so important to steer our business,” he says.
Sharing Data
Of course, location intelligence and other types of data are not just relevant within a single business—even a global reinsurer like Munich Re. Insurers and reinsurers are looking to both receive and share data with their clients and partners, as well. With the rise of natural and human-made risks across the supply chain, insurers want to know who their clients’ suppliers are—and where they operate—to accurately price risks.
Though it’s critical, the current state of data exchange is not where it should be, Siebert believes. “We have to improve,” he says. “Many of us are hoping for more open data initiatives where we have a common understanding of our risks or infrastructure.”
It is still difficult to obtain data sets that cover whole markets or whole countries, Siebert says. “Data availability is still sometimes a nightmare.”
At last year’s Reinsurance Association of the Americas (RAA) event, catastrophe response managers seemed to confirm this view. Attendees said they use NOAA and United States Geologic Survey (USGS) information as a baseline and would like other data sets to help build visibility.
“In many cases, major losses can occur due to the failure of one supplier in the value chain,” Siebert notes. “We try to visualize it, to get a better understanding [and] link the different supplier tiers according to the product chain.” To that end, Munich Re is working on creating a GIS-based solution for its clients by late this year or early 2020.
“We need a better exchange of information at all levels,” he says.
Going forward, such data will be increasingly important. A deeper understanding of location-based risk—associated with individual buildings and supply chains alike—can be an effective tool against loss from epic storms and other natural disasters triggered by climate change.
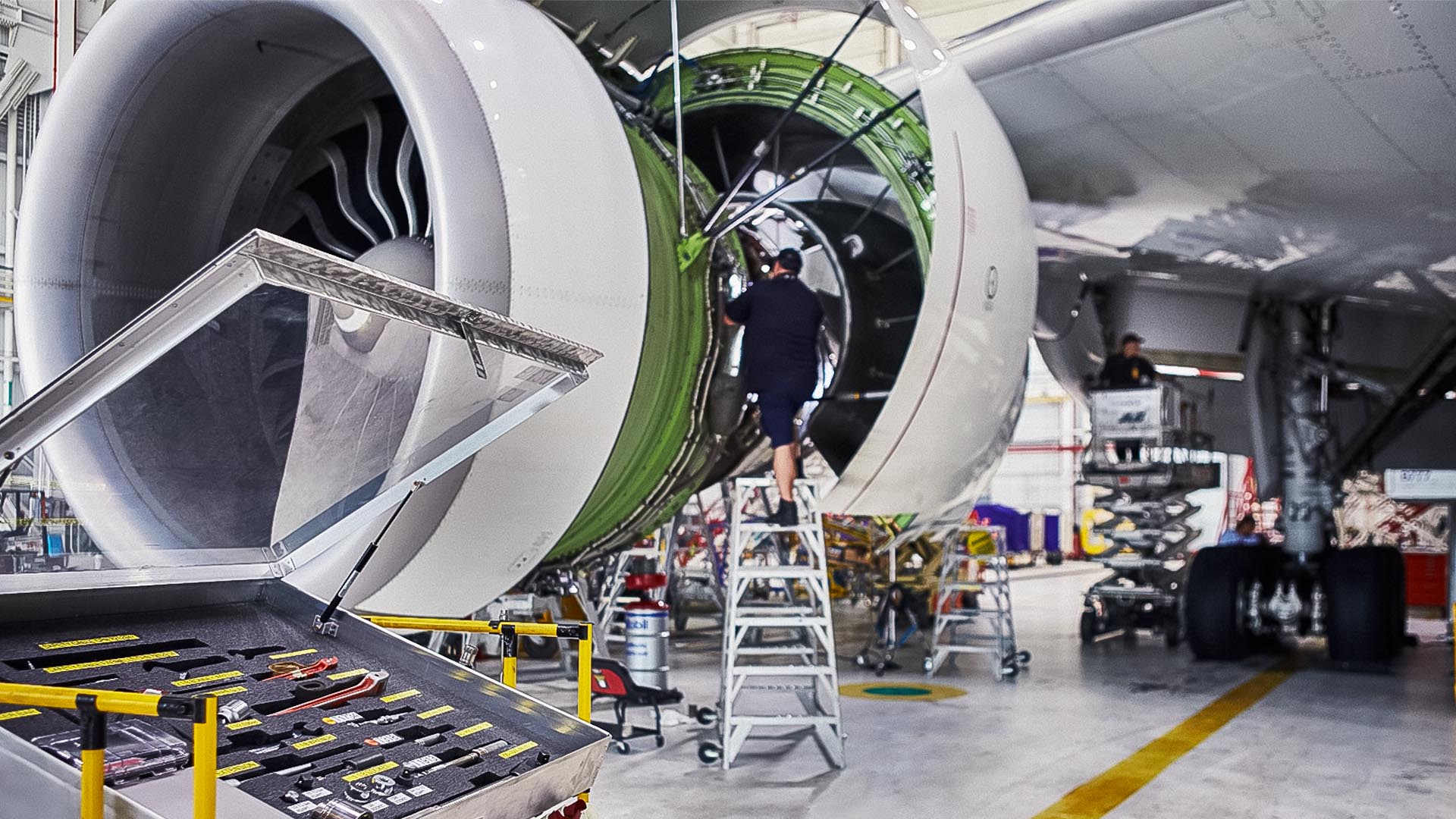
Location Intelligence Helps Keep FedEx on Time
By any measure, the numbers are staggering: 570,000 parts, 20,000 flights each month. FedEx manages it all with help from GIS.
It was late on a Thursday afternoon in November and FedEx had 160 jets in the air, flying to destinations around the globe. Most were on schedule, though a few were running several minutes late.
Each craft carried a bay full of items for eager customers from Shanghai to Memphis, Lisbon to San Francisco. Some of those packages actually included replacement parts for planes around the globe, and their on-time delivery was crucial to the carrier’s success.
Mark Yerger, vice president of material management at FedEx Express, knew where the grounded planes were and where to find the proper parts for them because of a sophisticated geographic information system (GIS). Through the system, Yerger could track up-to-the-minute progress for the fleet’s 386 jet aircraft and, with a click or two on his computer or hand-held device, drill down to learn just about anything he needed to know about a particular flight.
That level of spatial awareness, or location intelligence, empowers Yerger and team to maintain an impressive level of airplane health and availability. Last year, for instance, just 60 FedEx flights out of approximately 240,000—or .025%—failed to take off within 15 minutes of scheduled departure time because a replacement part wasn’t available in time.
Five Ps of Efficient Service
Yerger’s main concern is the operational status of hundreds of FedEx planes—and the parts that ensure their readiness. Those parts range from rivets that cost pennies to engines that cost millions of dollars. For an operation on the scale of FedEx to run cost-effectively, it can’t stock every part in every airport around the world. Instead, Yerger and his team rely on location intelligence to guide decision-making about parts and planes.
He describes their daily task as orchestrating a “very large aerial ballet” to ensure that the correct parts reach the correct planes quickly and efficiently. That choreography, he says, would be virtually impossible without the GIS-based smart maps at the heart of the FedEx tracking system.
Yerger uses five Ps to explain the ballet. “I have to have a part, a person, a plan, and a plane all in the same place at the same time,” he says.
To do that, Yerger often places a needed part on a FedEx jet that is carrying its usual cargo and is headed to the same location as the aircraft in need of repair. He can make that call by finding the correct part and then coordinating its delivery with flights in the air, or about to take off.
“If I can get that data in a very easily digestible way quickly, then I’m not going to make fire-drill calls,” he says. That often means he can avoid a last-minute rerouting or a “deadhead” flight that carries nothing but the replacement part. Those flights burn pricey fuel and pilot hours—without moving customer packages one mile.
Collaborating with IT
Yerger relies on a program FedEx has built and refined over the years, overseen by Bob Minford, the company’s vice president of airline technology. The program integrates GIS technology with the FedEx maintenance, repair, and overhaul (MRO) system, delivering location intelligence on smart maps. The program is available to FedEx executives, pilots, mechanics, flight planners, and just about anyone at the company involved in getting goods to their destination.
“Because of our scale and the global nature of our business,” Minford says, “we have a large number of our team members that are looking at this data.”
In order to deliver the world on time, those FedEx professionals need information quickly. “Whether they’re sitting in Global Operation Control managing all the operations, in Maintenance Operation Control, or at a maintenance shack waiting for a plane to come in, this gives them visibility” into the locations and dependencies among parts, people, and planes, Minford says. “It ties those relationships together by bringing all those disparate data sources into much better information [so] that they can make good decisions.”
That means mechanics can tap into the system using an iPad while in the hangar inspecting or working on a plane. “They could see all the manuals,” Minford says. “They could see everything about that aircraft, but they can also do every transaction that they can do on the desktop. So we’ve extended those capabilities from the desktop out to mobile devices.”
The bottom line, Minford says, is that the program allows our partners to concentrate on what’s most important.
“[W]ith the scale that we’ve gotten to and how these planes are constantly in the air, the geospatial tools really help many facets of the business to manage and to ensure that we simplify things.” That, he says, enables FedEx to “focus on the things that we have to focus on from a safety and an on-time service perspective.”
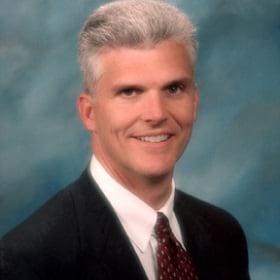
Having timelier access to more granular information, having the problems jump out of the screen… means that my maintenance specialists can absorb much more information more quickly than by looking at giant spreadsheets.
Mark Yerger, VP of material management at FedEx Express
Customers Want Speedy Delivery
“When it absolutely, positively has to be there overnight,” a FedEx tagline first deployed in 1978, has never been more apropos in the delivery and logistics business than right now.
While consumers still shop mostly in stores, the balance is shifting. The percentage of goods ordered online continues to grow, and with it, expectations for fast—sometimes even same-day—delivery.
That demand led to a 17 percent spike in parcel volume during 2017, according to a Supply Chain Dive article. Additional double-digit gains were predcited through 2020 across more than a dozen major economies. FedEx connects with 99 percent of the global GDP through 14 million air and ground shipments each business day.
Retail sales, one of the financial drivers of parcel companies, were estimated to rise almost 5 percent in 2018 over 2017’s nearly $5.7 trillion, according to the U.S. Census Bureau.
If global trade skirmishes escalate into trade wars this year, that could put a crimp on commerce. But the long-term trend is toward more goods being delivered quickly all around the world.
Long Haulers to Short Hoppers—Coordinating Moving Targets
Regardless of politics and trade negotiations, certain FedEx officials spend the majority of their day ensuring that the company’s fleet of almost 700 jets—ranging in size from long haulers like the Boeing 777 to smaller mid-range jets—are ready to fly around the clock.
Yerger relies on the company’s location intelligence system to track the fleet and make sure planes are where they are supposed to be, safely and at the right time. That’s no small feat when FedEx has aircraft circumnavigating the earth 20,000 times each month.
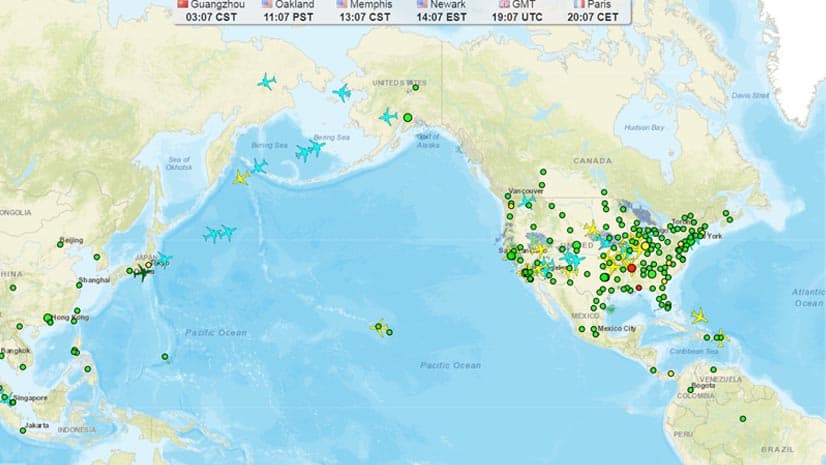
Coordinating FedEx maintenance worldwide with location intelligence
Like any executive who must make sensitive decisions in short order, Yerger looks to the GIS-powered system to find signals in the noise. As he explains, “The computer and the picture tell you what your biggest worries are, and/or what your easiest solutions are in a way that’s much easier for a human to digest.”
Planes on time, for instance, appear in green on his smart device or desktop, while those that are lagging are red. He can see flights all over the earth in one glance, or limit his view to aircraft associated with a particular region or airport.
That flexibility saves him and his fellow managers, as well as the mechanical staff that reports to him, precious minutes for other pressing decisions.
Data to Save Time
In essence, the FedEx system replaces a slew of documents with an integrated smart map, Yerger says.
“I don’t have to go thumb through 130 or 140 lines of a spreadsheet to figure out when did [the flight] depart, when was it supposed to depart, what’s the turnaround time, what’s the window, and when it’s expected back to [FedEx headquarters in] Memphis,” he explains.
One of Yerger’s primary responsibilities is avoiding the dreaded and costly AOG—an aircraft on the ground, unable to fly. During that November afternoon, Yerger checked the system to discover that only two of the planes in the air were behind schedule enough to cause concern. Both needed repairs that might not be completed in time for the scheduled departures. As a result, other planes might have to be used as replacements. In the industry, that’s called a tail switch.
On paper, the variables involved in the aerial ballet seem overwhelming. For instance, not all repairs are created equal. Some are mission critical and must be made before the airplane can lift off again. Others are less pressing, giving Yerger and team the luxury of time.
Then there are the parts themselves. FedEx manages more than 80,000 part numbers across its air operations. It keeps at least one part in each of about 575,000 bins at airports worldwide. Its nearly 700 planes visit 175 airports worldwide.
When one of those planes needs repairs and the five Ps aren’t aligned, Yerger’s team uses the logistics system to find the correct replacement part and coordinate its delivery to the aircraft’s next stop. Yerger likens the process to passing a hockey puck where a teammate will be instead of where he is.
To meet that “moving demand,” FedEx annually sends more than 850,000 shipments of parts. It’s a massive job made faster and more reliable by location intelligence.
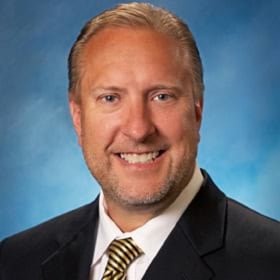
When I think about GIS, I think about a couple variables—not only [the] location of our aircraft, but GIS also provides us with time. And those are two variables that are extremely important to the business at FedEx.
Bob Minford, FedEx VP of airline technology
Artificial Intelligence Predicts Maintenance Needs
Yerger, Minford, and their FedEx colleagues know as well as anyone how important speed is to customer satisfaction and competitive advantage. The location intelligence system they rely on was built to help them make the right decisions faster.
And despite its success, FedEx continues to find ways to wring idle minutes out of its operations. The constantly evolving system, Minford says, now incorporates artificial intelligence, or AI, that forecasts when a plane needs replacement parts or a maintenance checkup.
AI’s predictive capabilities, combined with the geospatial programs that monitor where a plane is, amount to “almost the holy grail for a maintenance operation,” he says.
The company is also exploring maintenance innovations like using drones to perform airplane inspections that are cumbersome for humans to undertake. The top of a 777’s tail, for instance, can stand 60 feet above the ground. A mechanic piloting a drone with high-definition cameras now can detect hail or lightning damage faster than ever, while standing on the tarmac.
“As new things come up, we can just layer those relationships on,” Minford says, “and the map visualization simplifies it so that humans can understand it.”
That awareness of information tied to time and location, he says, allows Yerger and other FedEx professionals to act quickly on issues flagged by the system. “But they also see the big picture,” Minford adds.
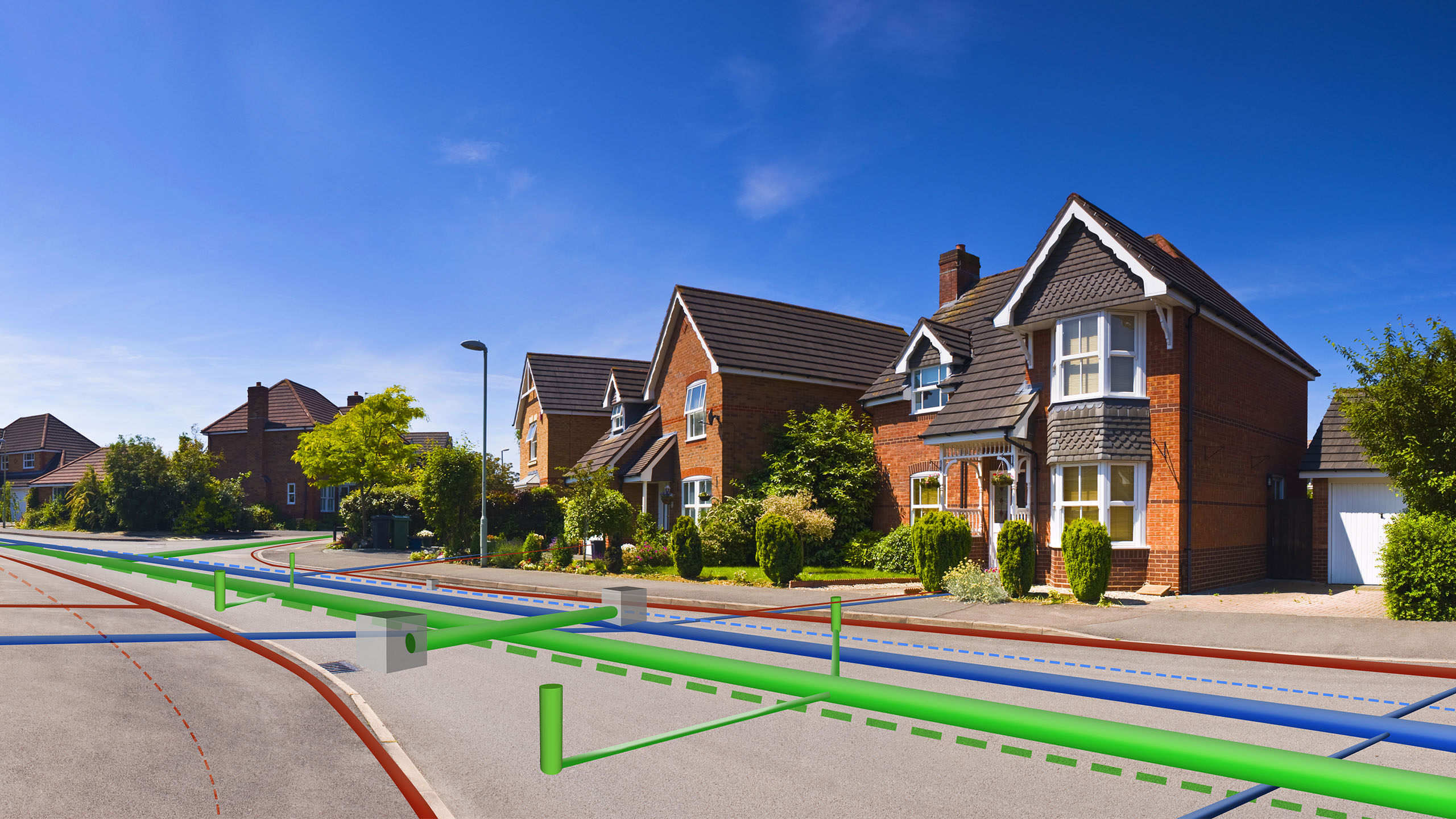
NJ Utility on Forefront with New Mixed Reality Application
The utility becomes one of the first agencies in the world to combine augmented reality with GIS technology for more efficient fieldwork.
A midsize utility in New Jersey has made the leap to adopt a cutting-edge mixed reality (MR) holographic application while blazing a path for other industries and businesses to follow.
Toms River Municipal Utilities Authority (TRMUA) may just be the first utility in the world to use mixed reality headsets to guide fieldworkers in locating underground utilities. This technological leap brings utilities and other companies with underground assets closer to realising an age-old wish: to see through dirt. The mixed reality solution is helping field technicians in Toms River close service tickets more quickly and avoid costly repairs.
“This is not science fiction anymore,” says Len Bundra, the IT/GIS director for the Toms River agency, and the person who saw the potential in a mixed reality application.
At its most basic, the Toms River system takes three well-established technologies and combines them into one brand-new application. All three are commercially available - Esri’s geographical information system (GIS), which stores location and attribute information on TRMUA’s underground assets; Microsoft’s Azure cloud-computing service; and Microsoft’s HoloLens. The three were integrated and customised by Meemim Inc., a Toronto-based company founded by Alec Pestov, who previously managed several startups.
Early results are sparking widespread interest, driven in part by the growing excitement and investment in mixed reality applications. As more agencies and organisations see the potential savings and increase in efficiencies and job safety, the use of hands-free mixed reality headsets may set the new standard for avoiding utility breaks while digging, and preventing errors when marking line locations on asphalt, concrete, or lawns.
Just a couple months into the pilot program, it’s hard to quantify savings. But in addition to minimising lost time, anything that lowers the chances of a utility main break is likely saving tens of thousands of dollars.
The first steps toward this technological leap came in 2005, when Bundra oversaw the installation of TRMUA’s GIS, which included precise (subdecimetre) data on the locations and sizes of more than 400 miles of wastewater pipes. With that rich database and other layers embedded in GIS, Bundra began to wonder how to create even more efficiencies in the field. He eventually found in Meemim a partner that wanted to explore the idea.
The partnership has turned out to be very useful, so much so that the dozens of utility representatives who have seen the TRMUA application in action have been impressed by its capabilities and ease of use and want to know more.
Ready to Experiment with Augmented Reality?
A few guidelines for the journey:
- Decide your use case. Identify a work process or business challenge that augmented reality/mixed reality (AR/MR) technology can improve or resolve.
- Survey the location of your assets with enough accuracy to suit your use case. (For Toms River, that meant achieving subdecimetre precision.)
- Ensure that your GIS database includes reliable attributes for your assets (size, installation date, material, diameter, etc.).
- Partner with other organizations or companies to share data and thus create a richer view of the world through the AR lens.
- Experiment, develop additional use cases, and share learnings with other agencies and partners.
Mixed Reality Technology across Industries
The use of mixed reality or augmented reality (AR) devices in work environments continues to grow.
Goggles, smart glasses, headsets, and helmets that project information, instructions, or images on the wearer’s field of vision are being used by manufacturing and retail companies that build equipment, repair machinery, or want to show customers what kitchens or homes will look like when completed. And the list of the technologies’ applications keeps getting longer.
In December 2016, the Wall Street Journal reported that companies were performing quality checks 20 percent faster and speeding up production by 25 percent with versions of the smart glasses. It also noted that Forrester Research, Inc., predicted that the number of US workers using smart glasses will grow from the current 400,000 to nearly 14.5 million in 2025. The research company also expects spending on smart glasses among large companies to increase from $6 million to $3.6 billion in the same period.
Those numbers do not surprise Cindy Elliott, head of commercial industry marketing for Esri. “The combination of GIS and augmented reality can address a lot of interesting business cases across industries,” Elliott says. “The technology is certainly powerful in outdoor settings like Toms River, but GIS and AR can also create efficiencies in warehousing, real estate, retail planning, and manufacturing.” (See the sidebar for one possible scenario.)
In essence, the use of mixed reality technology and GIS affords companies a new level of operational intelligence, which drives efficiency, increases safety, and can even inspire new service offerings. (Learn more about operational intelligence.)
As word has spread about the Toms River implementation, even utilities much larger than TRMUA—which has 435 miles of underground utility lines, 18 pump stations, and 47,000 ratepayers—are paying attention, and new partnerships are forming around the business potential of mixed reality.
While many utilities traditionally have kept a tight lid on data related to gas lines, electrical wires, and fibre-optic connections, Bundra sees that changing, thanks to the HoloLens project. “This technology is like a caveman fire for people to huddle around ” Bundra says. “When you put on the HoloLens, the more utility lines you see underneath you, the more utilitarian the product becomes. Now we’re suddenly huddling around the fire.”
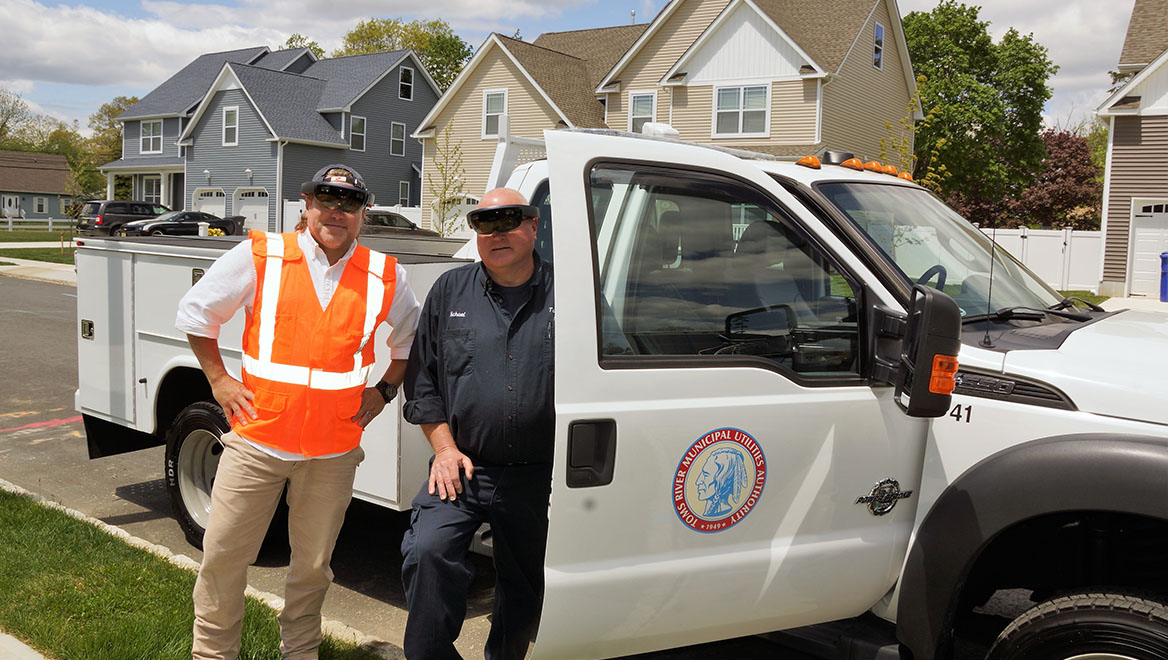
A Huge Potential for Savings
A simple scenario that was repeated several times during the first months of the Toms River project helps illustrate the increased efficiencies of GIS when coupled with the holographic headset.
The holographic headset includes audio, tiny cameras, movement sensors, and a system for confirming the wearer’s exact location relative to the underground pipes. While wearing the HoloLens transparent visor, utility workers see a mixed reality—including the real world in front of them as well as a holograph of the lines of wastewater pipes underground. The pipes are colour coded and projected to scale. With slight movements or audio commands, the wearers can summon screens showing relevant information.
This video offers a brief tour of the MR/AR experience. The relationships among the pipes are made clearer and the ability to gauge depth is much richer with the headset on, but the video conveys the basic functionality.
While wearing the headset, workers operate hands free, precluding trips back to the truck to get their bearings using two-dimensional maps of utility lines, or a tablet computer. And even more importantly, the technology allows fieldworkers to connect with remote colleagues—often an engineer in the office—who can see exactly what the fieldworkers see. This is accomplished through a simple Skype connection. So if the employee in the field—whether marking lines with paint or digging to fix or replace a line—is not sure how to proceed, an engineer or manager back at the office can highlight or circle certain areas where extra caution should be taken, and those marks will appear in real time on the fieldworker’s visor.
For instance, if the manager notices a grouping of utility lines, then the worker may be directed to stop using heavy equipment and start digging by hand until the issue is resolved. In the past, fieldworkers attempted to resolve these incidents over the phone or by summoning the manager from the office to the field—a slow and pricey process.
Having accurate GIS data and engineering help available at nearly all times can avert costly line breaks. A break in any utility line means that work comes to a screeching halt until repairs are made. Many of those problems occur because the aboveground markings are off. “So now a simple two-hour markup just turned into a $23,000 dig up and repair,” Bundra says.
And if the issue happens after business hours, the new application means that fewer employees need to drive to the site and risk exposure to open holes and heavy machinery at night.
But even the avoidance of small issues can add up to big benefits. For instance, a TRMUA worker on a routine assignment discovered a manhole cover that had been paved over. Accordingly, the next version of Meemim software will allow the wearer of the headset to mark the location electronically and then record an audio message to note the data discrepancies and any needed repairs.
From the Ground to the Conference Room
Len Bundra of Toms River Municipal Utilities Authority (TRMUA) sees many uses for GIS data and mixed reality. One involves coordinating the input of various agencies when planning buildings. Through HoloLens or another AR device, “You can have the New Jersey DOT sitting in Trenton, the water company sitting in Parsippany, [and] the MUA sitting in Toms River, all looking at the same mini-map from the same perspective, discussing what’s going to happen to this vacant lot in Toms River when it becomes a four-story condo,” Bundra says.
A Company’s Bridge to the Future
TRMUA’s data is precise. Wastewater pipes are plotted within a decimetre of their position. Indeed, the utility’s GIS helped emergency managers know exactly where wastewater lines were located after Superstorm Sandy blew away or covered up many of the landmarks in 2012.
For companies looking to bring mixed reality technology to their operations, indoors or outside, a richly detailed GIS database makes most applications possible. It can store information on the location of fixed assets, track mobile assets like trucks in real time, and monitor the conditions of anything equipped with a sensor. “Without a GIS, there’s nothing,” Bundra says.
That database of information allowed Bundra and Toms River to pioneer a different approach to operational intelligence, experimenting with MR technology that many people have heard of but few have actually used.
For his part, Bundra relishes the pioneering spirit of the project, as well as its early returns.
“I’m looking at this like it’s 1979 and I’m holding the first Walkman.”
This article was originally published in the global edition of WhereNext.
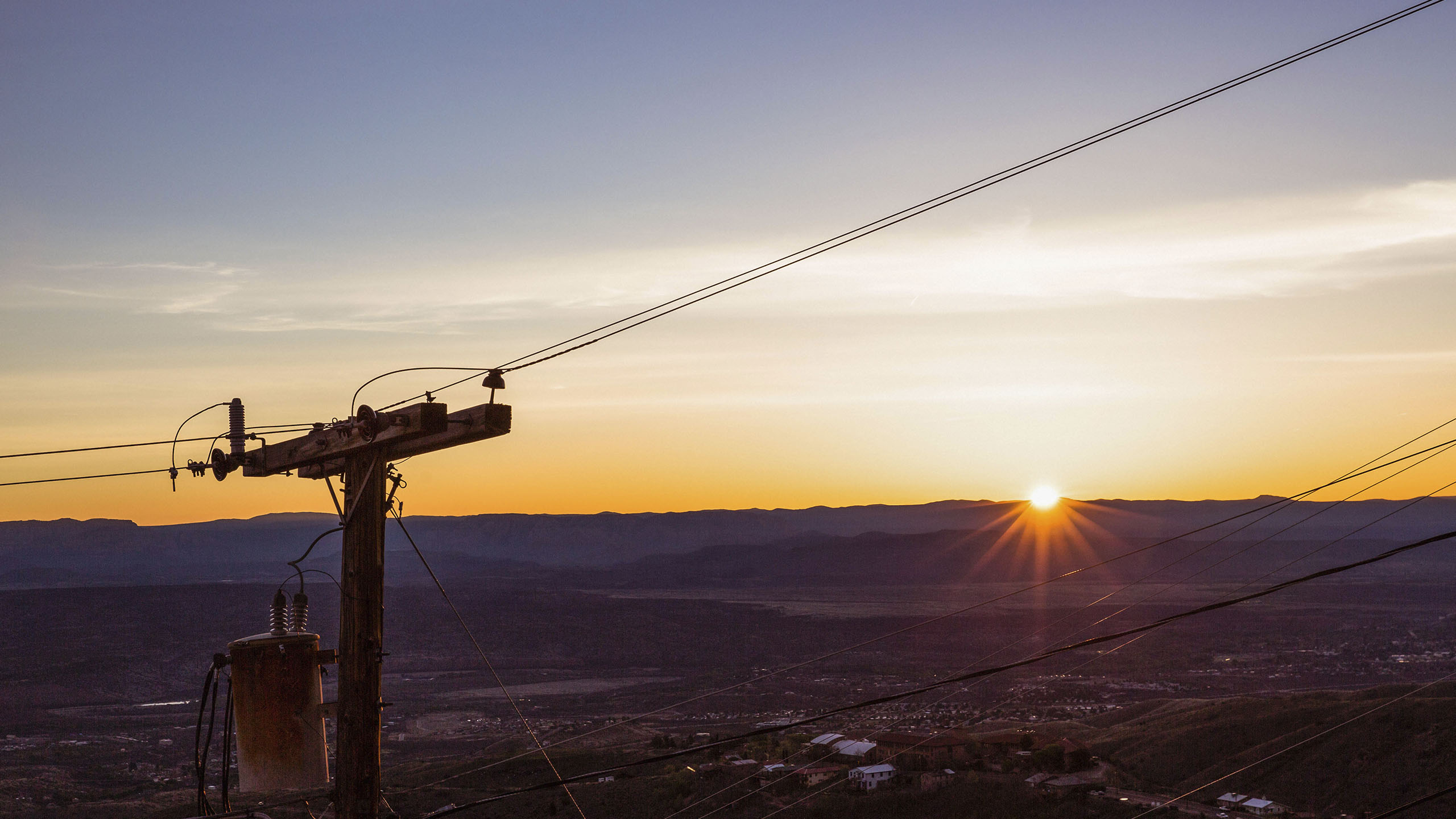
Get More from Your Assets: Five Steps to Operational Intelligence
Infrastructure-centric organizations have struggled to boost their operational IQ. A new plan shows a path to true operational intelligence.
At the dawn of 2007, Apple hadn’t released the iPhone, although Time magazine would later name it—along with the Palm Centro—a “gadget of the year.” The Glo Pillow debuted that year, sporting LED lights that gradually woke sleepers—but did not connect to the Internet of Things (today, even our eggs do).
In early 2007, consumers hadn’t met Amazon’s Kindle, which would go on to upend the publishing business. Boeing’s 787 Dreamliner was four years from entry into service.
How will our world change in the next 10 years? Will we see more sensors on more devices, and more operations-related information? Almost certainly. Will customer demands on business grow? Very likely. Will your business survive if it doesn’t innovate? Don’t bet on it.
In infrastructure-based industries, upstarts are beginning to write the story of the next decade. Renewable energy and distributed-generation companies are changing the way the grid operates. Telecoms are investing in networks to support autonomous transportation and manage billions of devices connected to the IoT, all of them generating data that can be converted into insight.
Many infrastructure-focused companies will struggle to survive against the upstarts. Data, along with the intelligence it provides, may be their salvation, but only if they know how to synthesize it.
The Case for Operational Intelligence
For infrastructure-dependent industries—including power distribution, manufacturing, mining, oil and gas, telecom, transportation, and water—today’s technologies deliver more data than operations managers can possibly handle at once.
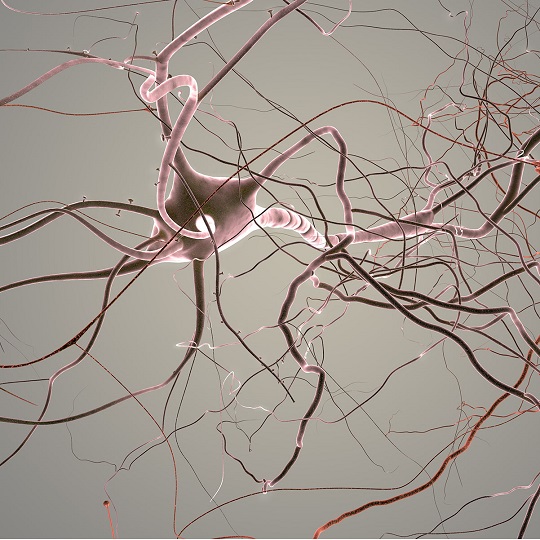
Throughout the industry, operations veterans have been retiring in large numbers. In their absence, we need a system that can replicate their collective wisdom. We need operational intelligence.
Even the short list of supporting technologies is long: AVL, DCS, MES, PLCs, SCADA, WFM. And because these systems often originate from different vendors and use disparate proprietary data models, integration is difficult. Point-to-point data integration is complex, costly, time-consuming, and often doesn’t happen—leaving operations personnel with a fragmented picture of business operations.
Most executives have seen this in practice. The operations manager sits in front of a bunch of monitors, each with a different view of the business. On one screen, a feed from the AVL system pinpoints the location of remote workers. On another is the local weather forecast. To the left are the day’s work orders, above which is a SCADA display. The desk is filled with paper reports from the field, detailing work that needs to be scheduled.
The manager must synthesize that information into three kinds of insight:
- What is happening
- Where it is happening
- What should be done about it
I know firsthand how rare that ability is.
Wanted: A Digital Stanley
Years ago, when I ran the operations division of a Northeast utility, one of my favourite employees was Stanley, the regional crew manager. Every night, Stanley had to make a decision. He had to choose whether to send the day crews home or keep them on overtime. If he dismissed them before a bad storm hit, for instance, it would mean longer outages, unhappy customers, and a flood of complaints to the regulator. If he kept the crews on overtime and no storm appeared, he would have wasted company money.
Here is what Stanley did.
He stood at the loading dock to smell the air. He checked the weather forecast. He considered our vulnerabilities—trees that hadn’t been trimmed, poles that were leaning and overstressed. He knew exactly where customers had been complaining. To make his decision, he organized this data in his head, by location. He assessed the risks. Then he would come into my office and tell me he was sending the crews home or keeping some on overtime. Stanley was doing spatial analysis.
In all the years I worked with Stanley, he was almost always right. His deep knowledge of his workers, local weather patterns, and our infrastructure—mixed with intuition—influenced his decisions and formed the core of our utility’s operational intelligence.
Then Stanley retired. All that knowledge, intuition, and understanding simply walked out the door.
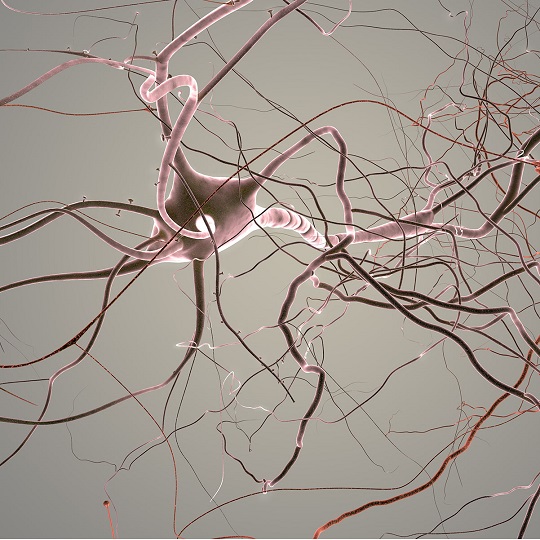
Many infrastructure-focused companies will struggle to survive against the upstarts. Data, along with the intelligence it provides, may be their salvation, but only if they know how to synthesize it.
My company wasn’t unique. Throughout the industry, people like Stanley have been retiring in large numbers. In their absence, we need a system that can replicate their collective wisdom. We need operational intelligence: technology that shows real-time asset performance, infrastructure locations, trouble tickets, weather conditions, customer calls and tweets, and field crew activity—in short, technology that would help monitor the many threats facing utilities. In addition to the ever-present threat of storms, utilities need to monitor aging assets, whose failure could lead to outages. Utilities need to guard against malicious attacks—both physical and cyber. And they must keep a wary eye on workers’ safety.
If we’d had the digital version of Stanley—one system dedicated to operational intelligence, easily viewable by location—we would have been much quicker to diagnose issues and launch appropriate responses.
Five Steps to Operational Intelligence
Many organizations struggle on the path to operational intelligence. And yet, throughout my career, I’ve seen companies improve their decision-making by building a better picture of what events are occurring in their service territory—and where.
Having seen the impact that event and location information can have on operations, I’ve developed a plan to help organizations improve their operational intelligence:
- Map Your Assets
A digital map is the baseline of a true common operating picture. When operations personnel understand the lay of the land, they enjoy a unified picture of everything inside and outside the operation. That becomes the foundation for decisions that lower costs, improve service, and promote safety.
- Connect Data across the Organization
A company looking to extract value from operational information must first bridge the gaps among data sources. A geographic information system (GIS) can be a valuable bridge for an infrastructure-based company, since GIS pulls data from all operational systems: SCADA, AVL, IoT-based sensors in the field, and more. GIS technology arranges that data on a map and makes the relationships among operational activities vividly apparent to managers and executives.
- Define Operating Rules
Not all operational information must be regularly monitored, and much of it must be refined before it can be useful. With GIS technology in place, a company can implement rules that filter noncritical data. Information that should be monitored monthly, for instance, won’t be displayed on a real-time dashboard, and conditions that indicate failure will appear in the operating picture only when they cross predefined thresholds.
- Share Intelligence
Decision-making occurs at regular and irregular intervals throughout an organization. Executives and managers must ensure that those decisions are based on consistent, reliable, and up-to-date information. That means dismantling the information silos that plague many organizations and opening data to create a broader view of the operating picture. Here, too, GIS plays a central role, distributing information and insight to decision-makers when they need them.
- Optimize Fieldwork
The final step in creating true operational intelligence is to optimize field operations by eliminating duplicate work and operational blind spots. Through a location-based information platform like GIS, fieldworkers see their assignments on any device, get turn-by-turn directions to work locations, and collect data about the work they perform—all of which feeds into the operations centre for real-time monitoring.
Intelligence in the Field
This five-step approach is helping infrastructure-based companies become more efficient, provide better experiences for their customers, and protect and expand revenue streams. I’ve seen the improvements time and again:
- By using GIS to understand the location and status of assets, Tennessee’s White House Utility District saves $1 million annually through early leak detection and more efficient use of personnel.
- A multibillion-dollar oil exploration and production company eliminates costly travel by using sensors to remotely monitor oil wells and analysing that information with GIS.
- A California county of more than one million residents analyses traffic information in real time and optimizes signals to keep drivers moving, improving the area’s quality of life.
- Seattle City Light, the tenth-largest public power system in the United States, feeds social media information into its GIS platform to better predict and respond to storms, boosting customer satisfaction.
No one can say for sure what the world will look like in 2027. But one thing we can say is that infrastructure-based companies that synthesize information more effectively will make better operational decisions—and increase their chances of thriving in the next decade.
This article was originally published in the global edition of WhereNext.